For me, there’s an incredible satisfaction in bringing steampunk creations like this mechanical watch and the blinking goggles to life. It’s a genuine passion project, where I get to dive deep into that unique blend of historical craftsmanship and imaginative engineering that defines the steampunk world. Every single detail, from the hand-painted finishes to the custom 3D-printed elements and the soft leatherwork, speaks to the sheer joy I find in making something tangible and functional. Watching the watch's delicate iris motion come alive and its tubes glow, or seeing the goggles blink with customized colors – it's just fantastic. That captivating movement, by the way, is all thanks to the clever integration of Arduinos and servos, which are a blast to work with. My love for steampunk really shines through in these pieces; I adore celebrating visible mechanics and that wonderful, anachronistic technology. It constantly pushes me to explore new techniques, whether it’s figuring out how to seamlessly hide battery packs or ensuring everything is easy to maintain. These aren't just props; they're expressions of the delight I get from combining diverse materials—foam, leather, and intricate electronics—to craft character-rich devices that truly transport you into a world powered by imagination and, well, steam.
​
​
​
​
​
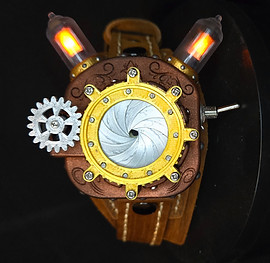


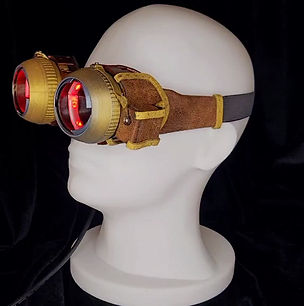
I'm excited to share these monumental 6-foot tall 3D printed sculptures of MechaGodzilla and Mecha King Kong, a project I proudly led for the Formlabs Hackathon. While the incredible 3D models were designed by ToyMakr3D, bringing these titans to life was a labor of intense dedication, involving many months of continuous printing on Formlabs machines, followed by countless hours of meticulous sanding and priming to achieve their commanding finish. This ambitious undertaking truly showcases my passion for large-scale digital fabrication, from the precise planning of each print segment to the hands-on artistry of post-processing, transforming raw 3D prints into polished, impactful physical representations. These pieces stand as a testament to the power of additive manufacturing and the incredible potential of collaborative fabrication, embodying my love for pushing the boundaries of what's possible in the world of 3D printing and model-making.
​
​​
​
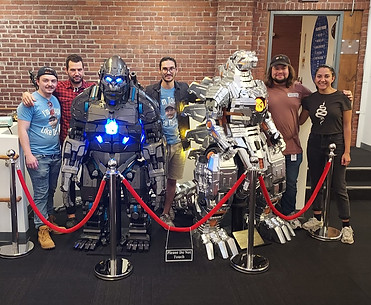



Bringing the iconic Powerloader to life as a full-size, wearable costume was an incredibly ambitious year-long endeavor that perfectly encapsulates my dedication to large-scale fabrication and practical effects. Constructed with a robust PVC frame and integrated PVC stilts, the structural integrity allowed for both dynamic movement and impressive stature, while the intricate shell was meticulously formed from cardboard. Every detail was designed for impact and realism: the torch boasts a rotating and illuminated feature, and the formidable pincers articulate up and down via a custom-engineered pulley mechanism, all activated with the push of a button. The immersive experience is further enhanced by loud, authentic stomping sounds synchronized with walking, truly bringing the machine to life. Presenting this challenging build at Boston Comic Con was a highlight, and I'm proud to say it is now displayed at Lesley University in their Game Production Lab, showcasing the culmination of extensive design, material mastery, and mechanical ingenuity that goes into creating functional, show-stopping pieces for my fabrication portfolio.
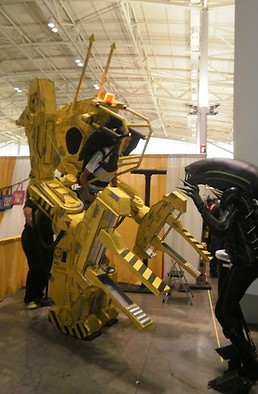
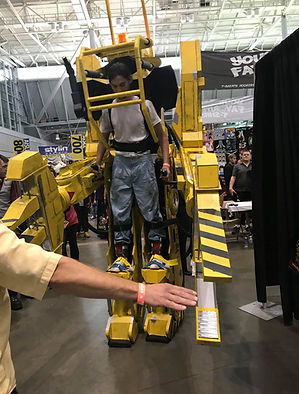
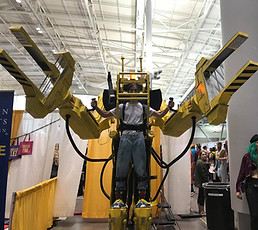

Building this full-size, wearable Space Marine armor was an immersive year-long odyssey, fueled by extensive 40K Warhammer research. The foundation of this formidable suit lies in its custom-engineered PVC stilts, providing both impressive stature and robust support, while the shell was meticulously crafted from EVA foam, balancing durability with wearability. Every detail was considered to bring this iconic warrior to life: the helmet and formidable gun are equipped with integrated lighting, casting an intimidating glow, and the suit even replicates the thunderous sounds of a Space Marine's steps as I walk. This project is a testament to my dedication to large-scale costume fabrication, blending material mastery, electronic integration, and a deep appreciation for source material to create a truly impactful and authentic piece for my fabrication portfolio.
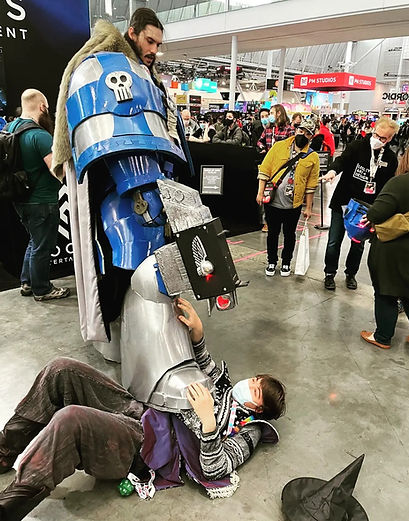
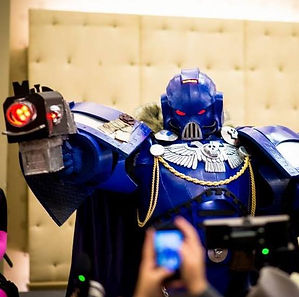

Crafting this full-size, wearable Iron Man armor was an incredibly ambitious year-long project that allowed me to push the boundaries of prop fabrication and integrated electronics. Meticulously constructed from EVA foam, the suit's iconic shell houses a complex system of features designed for both visual fidelity and dynamic functionality. The glowing eyes, hands, and chest repulsor bring the suit to life with vibrant light, while a network of servos intricately controls the opening and closing of the helmet, back flaps, wrist rockets, and calf flaps. All these dynamic elements are precisely orchestrated through Arduinos communicating to a remote control, showcasing my expertise in blending physical craftsmanship with advanced robotic integration. This suit stands as a testament to my dedication to detail and my ability to bring complex, interactive designs from concept to a fully realized, wearable piece for my fabrication portfolio.
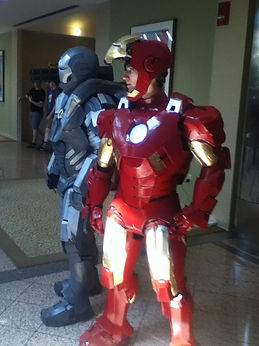

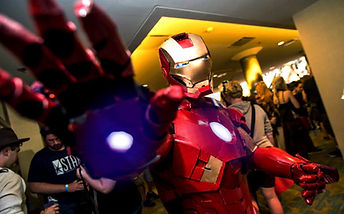

These projects represent some of my earliest and most ambitious forays into large-scale costume fabrication, foundational pieces that truly ignited my passion for the craft. My first Iron Man suit, meticulously built from EVA foam, featured glowing eyes, hand repulsors, and a lighted chest, demonstrating early experimentation with integrated electronics before venturing into the advanced servo and Arduino systems of later versions. Standing alongside it, the imposing 8-foot Hulk suit was a monumental undertaking, crafted from carved couch cushion foam shaped with an electric turkey cutter and then meticulously covered in fabric to achieve its distinctive skin. Wearing the Hulk suit also involved mastering 2-foot painting stilts, a unique challenge that expanded my fabrication skills. While these early works might be considered outdated now, they are invaluable testaments to my foundational learning, problem-solving abilities, and the sheer dedication required to bring such iconic characters to life through hands-on construction.